CNC plasma cutting is a technology that has revolutionized the world of metal fabrication. It involves using a plasma torch to cut metal of different thicknesses with a high degree of accuracy and precision. This technology is fast, efficient, and produces a clean-cut edge. It is becoming increasingly popular in the metal fabrication industry and is being used by businesses of all sizes, from small machine shops to large industrial manufacturing plants.
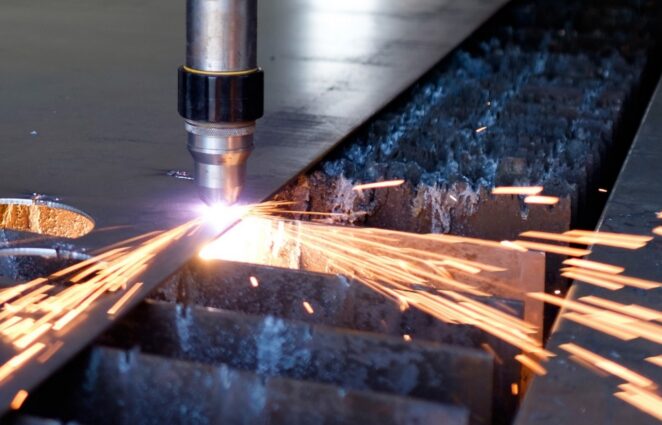
Advantages of CNC Plasma Cutting:
CNC plasma cutting has several advantages over traditional cutting methods.
– Firstly, it is much faster and more efficient. This is because the plasma torch can cut through metal much more quickly than traditional methods such as sawing, drilling or milling.
– Secondly, it is much more precise, and this is important when working with complex shapes and designs. The accuracy of CNC plasma cutting ensures that the final product is of a high quality and meets the required specifications.
– Another advantage is that it is a cost-effective solution. It allows for increased productivity and reduced labor costs, making it an attractive option for businesses looking to improve their bottom line. Additionally, the technology is very versatile and can be used on a wide variety of metals, including stainless steel, aluminum, and copper.
How CNC Plasma Cutting Works
CNC plasma cutting works by using a plasma torch to heat and cut metal. The torch consists of an electrode that is surrounded by a nozzle. When an electrical current is applied to the electrode, it ionizes the gas that is flowing through the nozzle. This creates a plasma arc that can reach temperatures of up to 30,000 degrees Fahrenheit.
The plasma arc is used to melt the metal, and high-pressure gas is used to blow away the molten metal. This creates a clean-cut edge, free from burrs or other imperfections. CNC plasma cutting machines are computer-controlled, and this allows for precise and accurate cutting. The cutting head can be programmed to move along a predetermined path, ensuring that the final product is of a high quality and meets the required specifications.
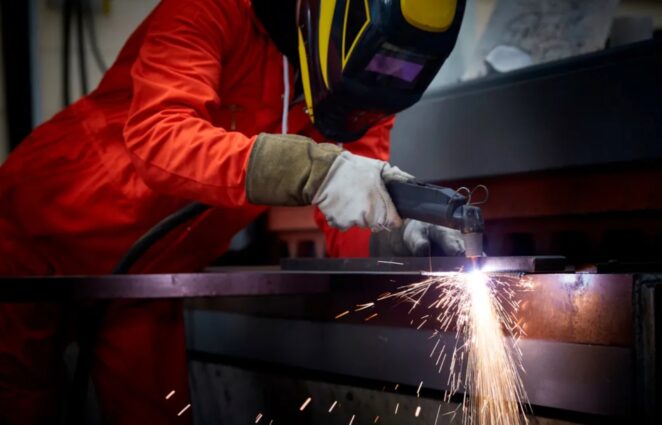
Applications of CNC Plasma Cutting
CNC plasma cutting has a wide range of applications in the metal fabrication industry. It can be used to cut complex shapes and designs, including circles, squares, and other geometrical shapes. It is also used in the manufacture of parts for machinery and equipment, including gears, brackets, and frames.
The technology is also used in the production of signage and lettering for buildings and vehicles. It can be used to create intricate designs and logos that are then applied to metal surfaces. Additionally, it is used in the production of custom metal artwork, sculptures, and decorative items.
CNC Plasma Cutting in the Machining Shop
CNC plasma cutting is becoming increasingly popular in machining shops around the world. In the machining shop, it is used to cut metal parts for machinery and equipment. It can also be used to produce custom metal parts for customers. Additionally, it is used in the production of signage and lettering for buildings and vehicles.
One of the reasons why it is so popular is its ability to cut through a wide range of materials. It can cut through materials that are too thick for traditional methods, making it a valuable tool for many industries. Additionally, it produces a clean-cut edge, which means that there is no need for additional finishing work. This saves businesses time and money, as they can produce a finished product in less time than traditional methods would require.
Another advantage is its ability to cut complex shapes and designs. This is particularly useful for businesses that require intricate parts for their machinery or equipment. CNC plasma cutting machines are computer-controlled, which means that they can be programmed to cut specific shapes and designs with a high degree of accuracy. This ensures that the final product is of a high quality and meets the required specifications.
In addition to its applications in the machining shop, it is also used in the automotive industry. It is used to cut parts for cars and trucks, including body panels and chassis components. Additionally, it is used in the production of exhaust systems and suspension components. The accuracy and precision of it ensure that these parts are of a high quality and meet the required specifications.
It is also used in the construction industry. It is used to cut metal parts for buildings, including structural components and decorative elements. Additionally, it is used in the production of signs and lettering for buildings. The ability to cut complex shapes and designs makes it an ideal tool for creating custom architectural features.
Overall, CNC plasma cutting is a technology that is changing the way we think about metal fabrication. It offers several advantages over traditional cutting methods, including speed, precision, and versatility. Its applications are numerous, and it is used in a wide range of industries, from the machining shop to the automotive and construction industries. As technology advances, it is likely to become even more efficient and versatile, further enhancing its capabilities in the metal fabrication industry.
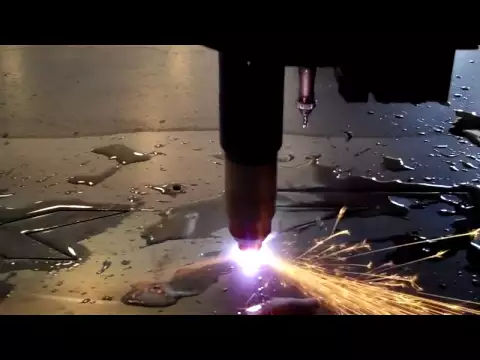
Conclusion
CNC plasma cutting is the future of metal fabrication. It is a fast, efficient, and cost-effective solution that produces a high-quality final product. It is becoming increasingly popular in the metal fabrication industry, and its applications are numerous. From the production of parts for machinery and equipment to custom metal artwork, this is a versatile technology that is changing the way we think about metal fabrication. In the machining shop, it is an essential tool that is helping businesses improve their bottom line and produce high-quality products for their customers. As technology advances, CNC plasma cutting is likely to become even more efficient and versatile, further enhancing its capabilities in the metal fabrication industry.